FORTEPRO
BAYERISCHER FORSCHUNGSVERBUND FüR TISSUE ENGINEERING UND RAPID PROTOTYPING
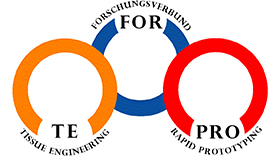
3D Strukturengineering
Arbeitsfeld:
Rapid PrototypingKnochen- und Knorpelstrukturen bestehen aus einer dreidimensionalen Matrix mit poröser Struktur, die mit induktiven Zellen aufgefüllt werden, und die im Zuge des physiologischen Remodellings durch körpereigenes Gewebe ersetzt werden sollen. Notwendig für diese Matrix ist - neben der exakten dreidimensionalen Form - die Verwendung eines Materials, das resorbierbar ist, also eine hinreichend feine Mikrostruktur besitzt, aber auch bei physiologischen biomechanischen Belastungen stabil bleibt, und zwar auch in der Anfangsphase, in der die Knochen- und Knorpelzellen noch keine eigene Stabilität besitzen. Im Teilprojekt RP 1 sollen deshalb optimierte 3D-Geometrien für den Bau von Custom-Implantaten zum Ersatz von Knochen- und Knorpelstrukturen generiert werden. Die Vorgaben bezüglich der Oberflächengeometrie und der einzusetzenden Materialien erfolgen dabei aus den Teilprojekten TE 1 bis TE 3, die Herstellungsverfahren werden in RP 2 und RP 3 entwickelt. Ausgangspunkt ist zunächst die Generierung der Oberflächengeometrie anhand der bildgebenden 3D-Datensätze von Knochen und Knorpel. Hierzu verwendet werden 3D-Ultraschalldatensätze, mit denen nicht nur die Knochenoberfläche (TE 2,3) sondern auch Knorpelstrukturen (TE 1) hochauflösend dargestellt werden können. Die Entwicklungsarbeiten in diesem Bereich konzen-trieren sich vorwiegend auf die Entwicklung neuer, an die Fragestellung angepasster Segmentierungsverfahren. Ergänzend dazu werden spezifische Informationen aus 3D-CT- bzw. holographischen Datensätzen mitberücksichtigt. Der auf diese Weise generierte 3D-Datensatz zeichnet sich durch eine exakte Abbildung der Oberflächengeometrie der zu rekonstruierenden Knochen- und Knorpelstrukturen aus. Zur Modellierung der Mikrostruktur erfolgen mathematische Entwicklungsarbeiten, die auf den aus dem Projektbereich TE bekannte Materialeigenschaften der Wachstumsmatrix und den biomechanischen Erfordernissen basieren. Ziel ist die Definierung einer optimierten Mikrostruktur, die bei bekannter Oberflächengeometrie und entsprechenden Materialeigenschaften des Matrixsubstrates auch die notwendige elastomechanische Stabilität besitzt. Vor der Überführung des so berechneten 3D-Gerüstes in den Modellbau erfolgt eine NURBS-basierte Optimierung des Datensatzes, dann wird der Datensatz in das für den Modellbau notwendige CLI-Format umgewandelt. Unter industrieller Kontrolle erfolgt die Fertigung von Prototypen in den Teilprojekten RP 2 und RP 3 mit den dort entwickelten und getesteten Verfahren und Materialien. Die für das Tissue Engineering geometrieoptimierten Custom-Implantate erhalten abschliessend durch CO2-Laserbearbeitung eine aufgerauhte Oberflächenstruktur, um nach Implantation im Gewebe eine Anlagerung der angrenzenden Gewebe zu fördern.