FOROXID
BAYERISCHER FORSCHUNGSVERBUND MULTISKALENDESIGN OXIDISCHER FUNKTIONSMATERIALIEN
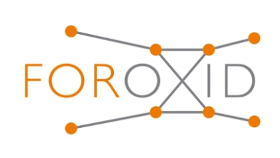
TP 2: Oxidkeramischer HC-Sensor
Arbeitsfeld:
Dicke oxidische SchichtenBei der Entwicklung der Automobil-Abgasnachbehandlung vollzieht sich hinsichtlich der sich im Abgasstrang befindenden Sensorik ein Wandel. Von Ende der 1970er Jahre bis weit in die 1990er hinein wurden lediglich potenziometrische Sonden, sogenannte Lambda-Sonden mit sprungartiger Kennlinie um Lambda=1, eingesetzt. Als Funktionselement dieser Sonden diente eine fingerhutförmige Keramik aus yttriumstabilisierten und daher ionenleitendem Zirkondioxid (YSZ). Seit Mitte der 1990er Jahre werden diese Sensoren allmählich ersetzt durch planare Ausführungen aus YSZ, hergestellt in keramischer Mehrlagentechnologie. Diese Sensoren sind nicht nur kostengünstiger sondern auch kleiner und schneller aufheizbar. Diese Herstellungstechnologie dient auch als Plattform für die ebenfalls seit Mitte der 1990er Jahre eingesetzte Breitband-Lambda-Sonde, die nach dem Grenzstromprinzip arbeitet. Darauf aufbauend wurden in Japan von zwei konkurrierenden Firmen Stickoxidsensoren entwickelt, die zur Steuerung der Abgasnachbehandlungseinrichtung eines direkteinspritzenden Ottomotors (erste Motoren in Deutschland: VW FSI) dienen. Solche Stickoxidsensoren werden von der Siemens AG als Komplettsystem (d.h. inkl. Elektronik und Systemintegration) kommerzialisiert. Dieser immer schnellere Wandel der Sensorik ist getrieben durch den ernormen Fortschritt bei der Entwicklung von Katalysatoren, der letztendlich auf die Einführung strengerer Abgasnormen wie EU4 und EU5 in Europa bzw. SULEV in Kalifornien zurückzuführen ist. Zusätzlich ist vorgeschrieben, dass On-Board die Funktionsfähigkeit des Abgasnachbehandlungssystems diagnostiziert wird. Der Automobilhersteller muss sicherstellen, dass ein zufällig ausgewähltes Fahrzeug auch noch nach langer Laufzeit die Emissionsvorschriften einhält. Falls dies nicht der Fall ist, wird der Fahrer durch eine Diagnoseanzeige aufgefordert, eine Werkstatt aufzusuchen. Es ist klar, dass diese On-Board-Diagnose (OBD) sehr zuverlässig arbeiten muss, da ein ungerechtfertigtes Aufleuchten der Diagnoseanzeige vom Kunden nicht toleriert wird und eine zu späte Diagnosebedarfsmeldung zu Strafen für den Kfz-Hersteller führen kann. Derzeit wird beim konventionellen Lambda=1-geregelten Otto-Motor die OBD durch eine zweite, nach Katalysator angeordnete Lambda-Sonde, der sog. Diagnosesonde durchgeführt. Dazu werden die Signale der Lambda-Sonde vor Katalysator (Regelsonde) und der Diagnosesonde verglichen. Man erhält damit ein Maß für die Sauerstoffspeicherfähigkeit des Katalysators, die mit der nachlassenden Konvertierungsleistung des Katalysators korreliert ist. Aufwendige Bewertungsmodelle führen dann zum Ergebnis der OBD. Da die OBD für zukünftige Abgasnachbehandlungssysteme nicht nur einen Katalysatordefekt sondern sehr präzise das Nachlassen der Konvertierungsleistung erkennen muss, wird das derzeitige Zwei-Sonden-Verfahren an seine Grenzen stoßen. Dies um so mehr als dieses Verfahren für mager betriebene Fahrzeuge (Diesel, Otto-DE) kaum angewandt werden kann. Es ist weiter zu berücksichtigen, dass über 90% der Kohlenwasserstoffemissionen während eines gesetzlich vorgeschriebenen Testzyklus in den ersten 60 s ausgestoßen werden, da in der Kaltstartphase die Rohemissionen am höchsten sind und sich der Katalysator noch nicht auf Betriebstemperatur befindet [6]. Optimal für die OBD wäre demnach ein im Kfz-Abgas einsetzbarer Kohlenwasserstoffsensor. Dieser muss schnell aufheizbar, hoch sensitiv und selektiv sein sowie eine möglichst kurze Ansprechzeit aufweisen. Der Sensor muss im rauen Kfz-Abgas über viele tausend Betriebsstunden langzeitstabil sein und in Großserie kostengünstig gefertigt werden können. Es soll ein Kohlenwasserstoffsensor entwickelt werden, der sowohl im Abgas von Dieselmotoren als auch im Abgas von Lambda=1-geregelten und direkteinspritzenden Ottomotoren eingesetzt werden kann. Dazu soll ein bestehendes Sensorprinzip erweitert werden. Der planare Kohlenwasserstoffsensor besteht aus zwei in Dickschichttechnik aufgebrachten strukturierten oxidkeramischen Funktionsschichten, die auf ein mit Heizer-, Abdeck- und Elektrodenschichten versehenes keramisches Substrat aufgebracht werden. Der Aufbau wird bei etwa 700°C im Abgas betrieben. Eines der beiden Sensorelemente ist katalytisch aktiviert. Der elektrische Widerstand dieses Sensorelementes ist vom Gleichgewichts-Sauerstoffpartialdruck des Abgases abhängig. Das andere Sensorelement ist nicht aktiviert und sein Widerstand reagiert stark auf Kohlenwasserstoffe. Aus dem Vergleich kann auf den Gehalt an Kohlenwasserstoffen im Abgas geschlossen werden. Die Genauigkeit des Systems würde stark erhöht werden, wenn es gelänge, den Sensor in einer Atmosphäre mit konstantem Sauerstoffgehalt zu betreiben. Für eine möglichst große Empfindlichkeit wäre ein Gehalt um etwa 1% Sauerstoff anzustreben. Eine geringe Querempfindlichkeit auf Sauerstoff erhält man bei etwa 10% Sauerstoff. Da dies im Kfz-Abgas nicht gewährleistet werden kann, soll das o.g. Sensorprinzip um eine integrierte Sauerstoffzudosierungseinheit erweitert werden. Diese soll aus einer elektrochemischen Pumpzelle aus YSZ oder CGO bestehen. Dabei ist natürlich zu beachten, dass der Vorteil des o.g. Sensorprinzips, der kostengünstige Aufbau aufgrund einfacher und zuverlässiger Technologien, nicht durch eine mechanisch aufwendige Konstruktion zunichte gemacht wird. Es ist daher geplant, den kompletten Aufbau in einer konventionellen Folien- und Dickschichttechnik zu realisieren. Zusammenfassend lässt sich feststellen, dass das Endziel des Projektes in der Bereitstellung eines abgastauglichen Kohlenwasserstoffsensors für fette und magere Abgasatmosphären ist. Dabei werden viele oxidische keramische Werkstoffe eingesetzt, die zusammen zu einem in wesentlichen Punkten verbesserten Bauelement führen, das die technischen und wirtschaftlichen Voraussetzungen für den Einsatz in Großserie erfüllt. Es ist also weder ein Ziel des Projektes, Materialeigenschaften zu erforschen und physikalische Modelle dafür zu entwickeln noch ist es ein Ziel des Projektes, Werkstoffparameter eines Materials zu optimieren. Vielmehr ist es aus materialwissenschaftlicher Sicht Ziel des Projektes, oxidische Werkstoffe miteinander so zu kombinieren, dass sie zu einem verbesserten Bauelement führen. Dabei müssen chemische und thermo-physikalische Wechselwirkungen, die bei der Herstellung und beim Betrieb auftreten können, verhindert werden.
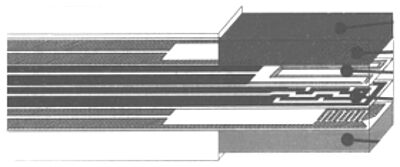