FORWERKZEUG
BAVARIAN RESEARCH ASSOCIATION FLEXIBLE TOOLS
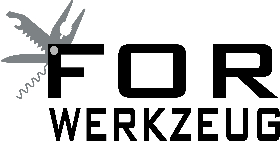
A2: Method for predicting the wear on sheet metal forming tools produced by alternative manufacturing technologies
In this research project, a method is developed for carrying out quantitative calculations of the degree of wear on tool elements used in sheet metal forming processes. The project is based on knowledge gained from EFB project AiF 12646N ‚Application of numerical methods for evaluating the degree of wear on tools used in sheet metal forming processes’. It is focused on RP processes and dies which can be produced out of alternative materials. The application of RP processes in the area of tooling is only economical when the number of pieces to be produced is sufficient. Unexpected and premature wear on the dies will result in further costs for maintenance or the manufacture of new tools; and thus RP processes may not be economical anymore. Therefore, in order to chose a suitable RP process, it is inevitable to have detailed knowledge on the wear mechanisms and properties of the dies against the geometry of the dies and the combination of materials. For the first time in a wear simulation, also the number of pieces to be produced is considered besides the combination of materials component and tool. This is possible due to the quantity-dependent determination of the wear coefficient. The wear prediction is carried out with iterative calculation software (REDSY) which was developed at utg and bases among other things on results of the forming simulation (PAM STAMP). For a successful calculation with REDSY, the quantity-dependent wear coefficients have to be determined and the implemented wear mechanisms have to be adjusted to the RP processes. Subsequently, the model is calibrated in experimental tests by carrying out forming tests with a workpiece whose shape is simplified and axially symmetric. The wear mechanisms and properties of the dies are investigated with respect to different combinations of the materials of blank and tool, and the particular quantity-dependent wear coefficient is determined. A follow-on composite tool is used in order to carry out the required and extensive forming tests at a low expense of time and cost. Objective of this project is to simulate and predict the quantitative tool wear of any part geometry for the investigated combination of materials. The verification and validation of the model is carried out by linking it to the subproject ‘Alternative Processes and Materials for Flexible Tool elements’; with the help of a complex geometry, the real wear progress is compared to the results from the simulation.